Remember, data is not just the street signs, it is the GPS
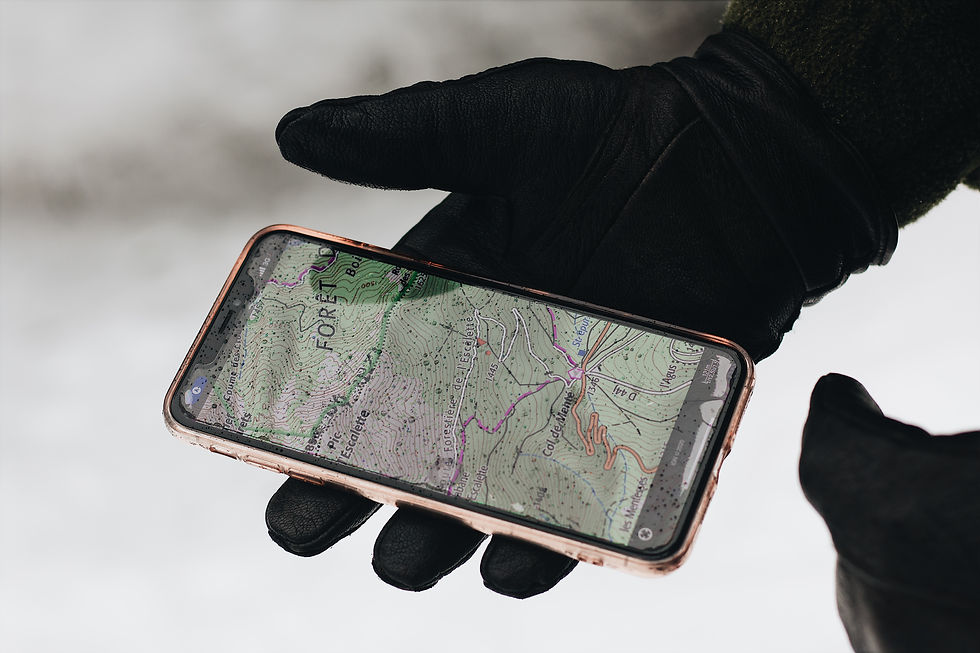
Use of GPS in Construction Industry-The expression “everything old is new again” can be aptly applied to The Global Positioning System (GPS). Typically, as technology finds a home in the construction industry, its new and better uses are inevitably discovered over time. In recent years we have seen that natural progression with GPS technology. From simple location tracking, GPS has developed to something that could actually change the way we navigate our world.
Construction companies are able to eliminate unauthorized vehicles and assets use with a GPS fleet management solution. With staff taking company vehicles home, the construction organizations needed a technique to efficiently monitor vehicle usage after hours and track the assets at the worksite too. By managing personal vehicle use, the organizations saw increased employee productivity, reduced fuel costs, and savings from their insurance provider. Tracking your vehicles & equipment can potentially save you 10 to 15 percent on your insurance premium.
Use of GPS in Construction Industry?
Managing a construction fleet used to involve tons of paperwork and phone calls. In the past, fleet managers had to manually calculate important data such as fuel used, miles driven, and more. As telematics technology has advanced, the duties and role of a fleet manager have dramatically changed. GPS tracking technology for construction companies has streamlined the process of dispatching drivers to jobs, tracking vehicles, and fleet management in general.
How GPS Tracking Improves Productivity and Efficiency?
Any industry that has a fleet can benefit from GPS tracking, and that is certainly true for the construction industry. Below are some key ways GPS can help your construction company improve productivity and efficiency.

GPS walking Indoors
Historically, GPS mapping has been predominantly used in construction to give the exterior view of a building in progress. However, the technology is being refined and purposed for indoor use as well. The resulting indoor positioning systems offer a number of benefits, like keeping track of the locations of objects or people inside a structure. The indoor GPS system has the ability to accurately and dynamically locate people and assets in real-time, from early Jobsite operations through to post-construction services for building owners.
Real-Time Tracking
Indoor positioning allows supervisors to pinpoint the precise location of any piece of equipment or worker on-site at a single glance. The indoor map is kept up to date as the job progresses. Therefore, it can provide a holistic, real-time view of the project to help ensure everything runs smoothly. It also provides a much-enhanced understanding of interior configurations and room layouts. It allows for better planning and more precise measurements, which thanks to GPS, do not need to be taken manually—a simple walkthrough is sufficient.
Location Awareness Technology
It is not just buildings in progress that will benefit from the next evolution of GPS. More projects are implementing “location awareness” technology. One day, navigating the interior of a high-rise campus could be as easy as finding the nearest coffee shop using GPS. We almost take for granted how easily we can find our way around city streets aided by GPS. If we could always know where we are and where we are going—even indoors, it will not only change construction but our perception of the entire world.
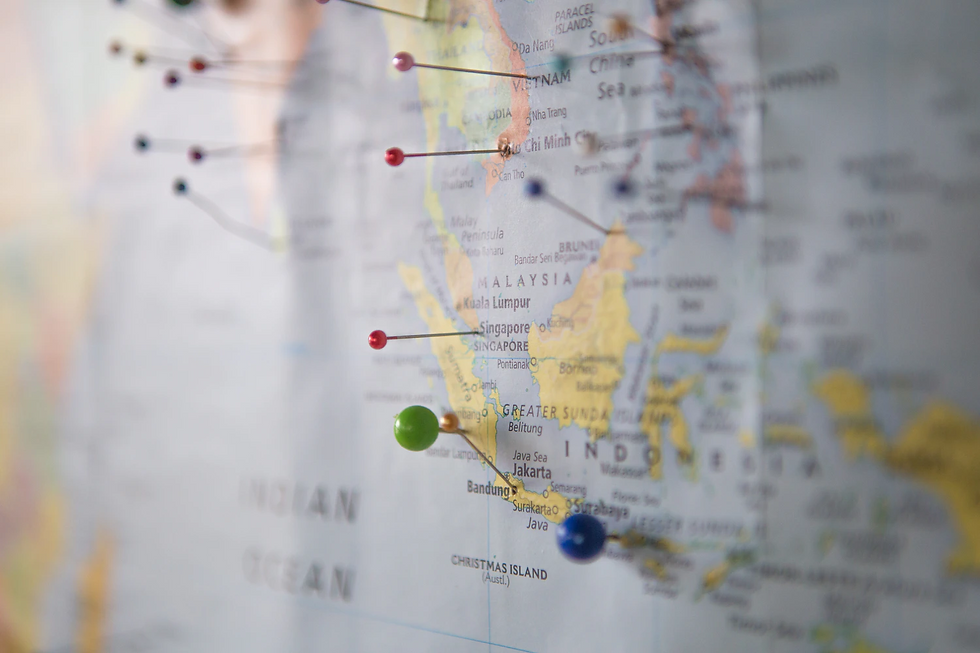
Streamline Workflow and Allocation
Downtime costs your construction business money. When using paper-based records, assets may sit idle between jobs, even if only for an hour. It may not seem like a lot at first glance, but multiply that hour by all your business’ assets. Then think about all the jobs you take on in one year, and you will see how much time, and money, you may be losing. Sitting idle between jobs is not the only way your assets experience costly downtime. They may be sent to a job where they are not needed. Either way, when your equipment is not where it needs to be, it is not making your business money.
GPS fleet tracking lets you know when an asset is available so that you can send it to the right job site with the shortest amount of idle time. You can track all your assets in real-time, so you always know which ones are where, and get a complete picture of what assets are needed on all your job sites.
Tracking Your Crews and Billing Assistance
It may not happen often, but there may be times when your crews are not where they should be. GPS tracking can let you know where your vehicles and the assets related to a specific job are in real-time. You can set up geofencing that lets you know when your crew enters or leaves a specific area. You can use this information to keep track of how many hours they worked in a specific area.
Monitoring electronic time lots and allocating assets and crews based on real-time insights can ensure that driver hours reporting is accurate and can help you control over time. You can use GPS tracking data to record their hours based on when they arrive at the job site. You can also use it to control timesheet fraud. Timesheet fraud happens when your crew records more hours than they worked. This not only costs you money but can also cause you to bill your customers incorrectly. This can all be avoided by replacing paper logs with a telematics system that lets you pull reports on start and finish times, hours and days worked, average hours, and more.
Accurate Estimation and Budgeting of Expenses
Using a GPS telematics solution can make your payroll and cost estimates more accurate. You will know how much time your crews spent on the road, how much on the job, and how much was on breaks, so your payroll with being more accurate. You can also keep track of fuel expenses by seeing exactly how much fuel your crews use on each job and overall. Using this and other GPS data lets you estimate future costs based on previous costs. And since all the tracking is done remotely and stored securely, you can do this all on your laptop, tablet, or computer.

Reduced Wear and Tear on Vehicles
Ensuring your vehicles and equipment are maintained and in optimal working condition can save you money, reduce risk, and decrease downtime, especially unexpected downtime. It costs less to maintain a vehicle than it does to repair it. Well-maintained vehicles also run better, so your fuel costs may be lower.
Well-maintained vehicles are also less likely to be involved in accidents or breakdown unexpectedly. This is safer for your crew and for other drivers on the roads. And when a vehicle breaks down unexpectedly, your crew is instantly less productive. Scheduling preventive maintenance for your vehicles and equipment keeps your crew productive, your projects on time, and your customers happy. It would not impact your scheduling because you can either schedule your maintenance during slower times or plan around it.
The benefit of GPS in the construction industry can be seen in a construction fleet of any size. You can manage every stage of projects by monitoring asset utilization and tracking equipment. You will have the peace of mind that comes with knowing your projects and your business is operating as efficiently as possible. There are many other savings and improvements benefits of GPS trackers for construction companies such as consistency with worksite conditions, Enhanced finding and deploying, and so forth.
Once you find the right GPS tracking system for your constructing company, setting the system up is not any more difficult since the device has already been well-tested, approved, and ready to use. What you only need is a Smartphone or laptop or computer with an Internet connection along with some basic knowledge of operating them.
Comments